What is Porosity in Welding: Recognizing Its Reasons and Enhancing Your Skills
Wiki Article
Unraveling the Secret of Porosity in Welding: Tips for Decreasing Problems and Taking Full Advantage Of Quality
In the intricate globe of welding, porosity continues to be a persistent challenge that can considerably affect the top quality and honesty of welded joints. As we delve into the midsts of porosity in welding, revealing the keys to its avoidance and control will certainly be paramount for professionals seeking to understand the art of high-grade weldments.Recognizing Porosity in Welding
Porosity in welding, an usual issue encountered by welders, refers to the visibility of gas pockets or gaps in the bonded product, which can jeopardize the stability and quality of the weld. These gas pockets are generally trapped throughout the welding process because of various factors such as inappropriate securing gas, polluted base materials, or incorrect welding criteria. The formation of porosity can compromise the weld, making it vulnerable to cracking and deterioration, eventually resulting in structural failings.Comprehending the source of porosity is essential for welders to effectively stop its incident. By recognizing the relevance of preserving proper gas protecting, guaranteeing the tidiness of base materials, and maximizing welding settings, welders can significantly minimize the possibility of porosity development. Furthermore, making use of methods like preheating the base product, employing proper welding techniques, and performing extensive inspections post-welding can additionally aid in reducing porosity defects. Generally, an extensive understanding of porosity in welding is crucial for welders to create high-grade and resilient welds.

Typical Reasons of Porosity
When checking welding procedures for potential high quality problems, recognizing the common root causes of porosity is crucial for keeping weld honesty and stopping structural failures. Porosity, defined by the visibility of tooth cavities or gaps in the weld metal, can considerably endanger the mechanical residential or commercial properties of a welded joint. One typical source of porosity is inappropriate securing gas protection. Insufficient protecting gas circulation prices or incorrect gas combinations can bring about climatic contamination, causing porosity formation.
One more prevalent reason for porosity is the presence of dampness and impurities on the surface area of the base metal or filler material. When welding materials are not properly cleansed or are revealed to high levels of humidity, the evaporation of these impurities during welding can create voids within the weld grain. In addition, welding at incorrect parameters, such as excessively high traveling speeds or currents, can generate too much turbulence in the weld pool, capturing gases and causing porosity. By dealing with these common reasons with proper gas securing, material read here prep work, and adherence to ideal welding parameters, welders can minimize porosity and boost the high quality of their welds.
Methods for Porosity Prevention
Applying efficient safety nets is crucial in decreasing the occurrence of porosity in welding procedures. One strategy for porosity prevention is ensuring appropriate cleaning of the base steel prior to welding. Impurities such as oil, oil, rust, and paint can lead to porosity, so thorough cleaning utilizing ideal solvents or mechanical methods is crucial.
An additional secret preventative step is the option of the best welding consumables. Making use of top quality filler products and shielding gases that appropriate for the base steel and welding procedure can dramatically minimize the risk of porosity. In addition, maintaining appropriate welding criteria, such as voltage, present, take a trip rate, and gas flow rate, is crucial for porosity prevention. Differing the suggested setups can result in incorrect gas insurance coverage and poor blend, leading to porosity.
Additionally, utilizing appropriate welding strategies, such as keeping a this page regular traveling rate, electrode angle, and arc size, can aid stop porosity (What is Porosity). Appropriate training of welders to guarantee they comply with best practices and quality control treatments is additionally crucial in decreasing porosity flaws in welding
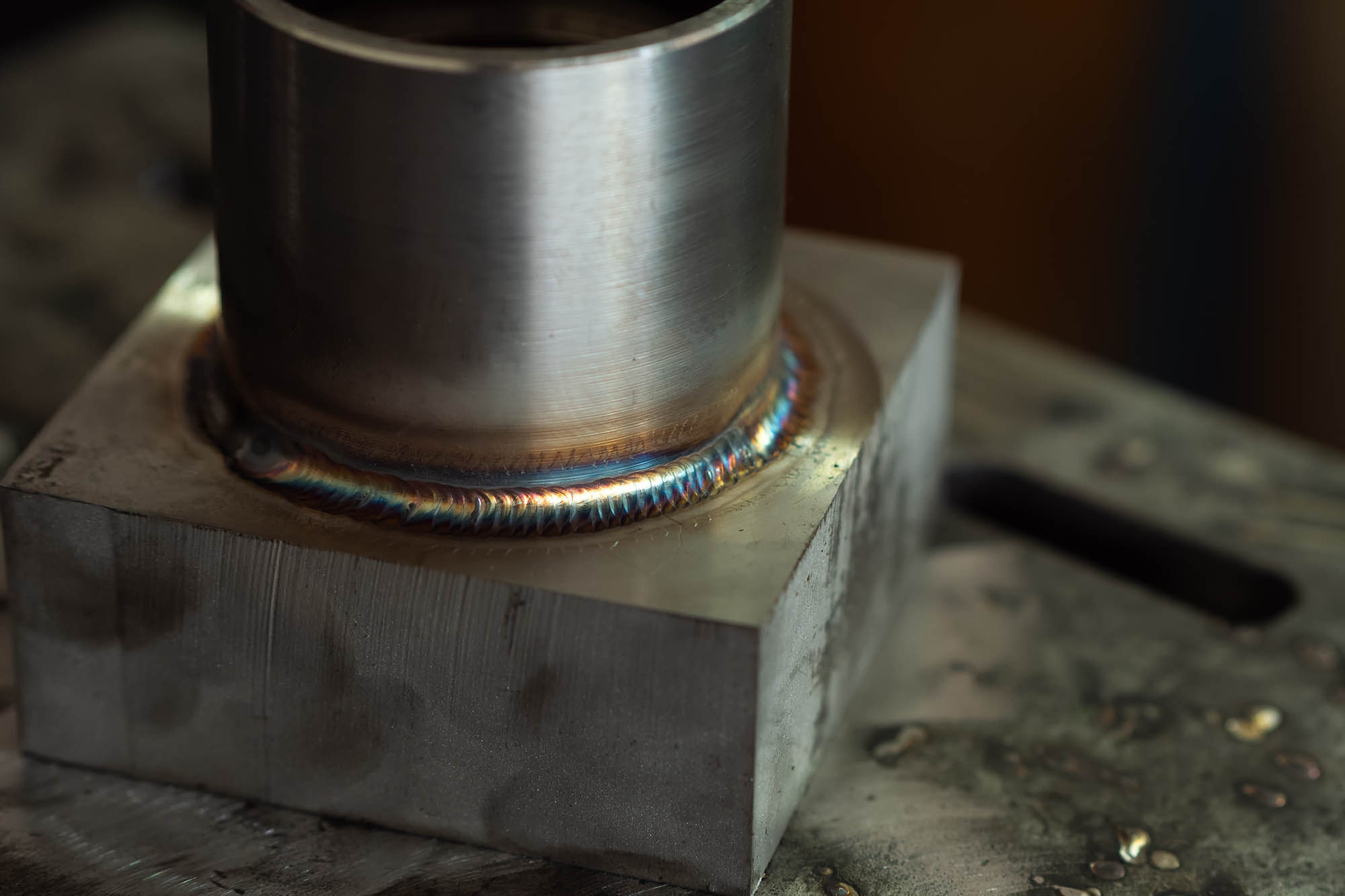
Best Practices for Quality Welds
Guaranteeing adherence to industry standards and correct weld joint prep work are essential elements of achieving consistently high-quality welds. Along with these fundamental actions, there are a number of best techniques that welders can apply to additionally improve the quality of their welds. One trick technique is preserving browse around here proper cleanliness in the welding location. Impurities such as oil, oil, rust, and paint can negatively affect the top quality of the weld, causing problems. Extensively cleaning up the workpiece and bordering area before welding can help alleviate these issues.One more finest technique is to carefully select the suitable welding specifications for the certain products being signed up with. Correct criterion selection ensures ideal weld penetration, combination, and general high quality. Utilizing top notch welding consumables, such as electrodes and filler steels, can dramatically influence the last weld top quality.
Value of Porosity Control
Porosity control plays an important role in making certain the stability and top quality of welding joints. Porosity, characterized by the existence of tooth cavities or voids within the weld metal, can considerably compromise the mechanical homes and architectural honesty of the weld. Too much porosity weakens the weld, making it more susceptible to fracturing, rust, and total failure under functional lots.Efficient porosity control is important for maintaining the preferred mechanical residential properties, such as toughness, ductility, and durability, of the welded joint. What is Porosity. By lessening porosity, welders can improve the general quality and reliability of the weld, making sure that it meets the efficiency needs of the designated application
Additionally, porosity control is important for achieving the preferred aesthetic appearance of the weld. Extreme porosity not only damages the weld but also diminishes its visual appeal, which can be crucial in markets where visual appeals are vital. Appropriate porosity control methods, such as utilizing the right shielding gas, regulating the welding parameters, and making sure appropriate cleanliness of the base products, are vital for generating high-grade welds with marginal issues.

Final Thought
In final thought, porosity in welding is a common flaw that can jeopardize the quality of the weld. It is essential to manage porosity in welding to make sure the integrity and strength of the final product.Report this wiki page